MF type (Flat core linear motor/Long travel/High power)
Introduces the type MF, providing high power and long stroke using flat motor with core.

MF type
Long stroke & high-power using flat motor with core.
Maximum stroke: 4 m
Maximum speed:Â 2500 mm/s
Related positioning accuracy: ± 5µm
Maximum payload: 7 to 160 kg
Feature
01 High speed, Long Travel, up to 4 meters!
The ultimate appeal of linear motor single-axis robots is that there is no critical speed limits such as with ball screws. There is no reduction in the maximum speed even when traveling long distances. Moreover, the maximum stroke is a standard setting of up to 2m on the MR type and to 4m on the MF type. The cycle time in particular for long distance conveyance has been drastically improved.
Movement time comparison of linear single-axis PHASER
and single-axis robot FLIP-X
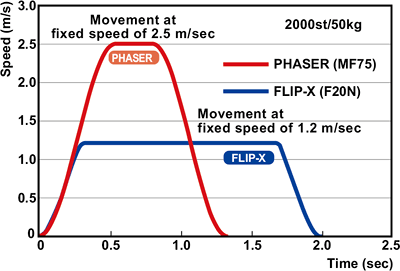
02 High Payload on MF type Maximum payload: 160kg
The MF types which employs flat magnets has a maximum stroke length of 4m. Payloads can be conveyed over long distances. The maximum payload has been increased from 100 up to 160kg and can be conveyed with high accuracy at high speeds. (In the MF types, the maximum speed is limited in some payload ranges.)
03 Lower Application Cost Due to Linear Motor Features
Linear motor types are more effective in lowering costs when coveying payloads at high speeds, over long distances with greater repeatability.
System feedback is provided by proprietary magnetic scale developed by Yamaha.
04 Double Carriges Standard on all Modules
The MF series supports double carriers as a standard feature which allows configuring a system with space-saving efficiency.
This arrangement yields lower costs and better tact time as compared to using 2 single axis robot units.
Benefits are shorter setup times, addtional axis combinations are no longer needed, and tools can be jointly used, etc. (Collision prevention program can also be utilized on RCX series controllers.)
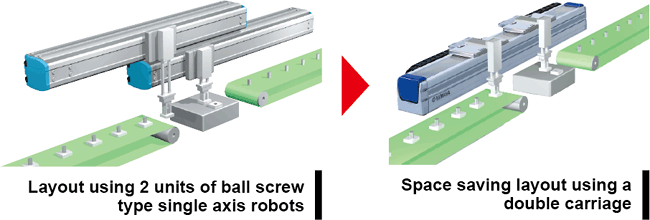
05 Effective use of stroke
Linear motor type single-axis robots also contain an internal coil inside the table as a drive unit component that eliminates inner dead space and maximizes the stroke. The unit is also bilaterally symmetrical so there is a higher degree of freedom in the robot layout.

06 Quiet with a long service life
Unlike ball screw type robots, there are few sliding and rotating sections so the operation is amazingly quiet. Moreover the coil and magnet do not make contact so there is no wear and the robot can be used for extended periods.
07 Linear scale made by YAMAHA
YAMAHA used its own superb magnetic signal detection linear scale technology.
Magnetic type scale is ideal for harsh environments
Yamaha’s magnetic scale is resistant to dirt and grime and can be used in places partially exposed to grease and cutting oil.
Semi-absolute specifications
Using semi-absolute specs eliminates the need to make a large return to origin movement after turning on the power (carriage moves a maximum of about 76 mm when loading the signals). The semi-absolute scale acquires the current position by loading signals recorded on the linear scale.Â
High resolution to 1µm
Magnetic signals recorded from the magnetic scale are detected and interpolated to achieve a highly accurate of resolution 1µm.
Lower costs
Making the scale in-house and internalizing it in the robot provides long travel position feedback at reasonable cost.Â
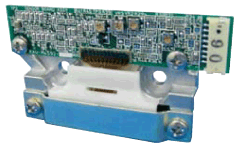
Repeated positioning accuracy +/-5µm
A fully-closed control system provides constant feedback of the carriage position to attain highly accurate and stable positioning. Backlash is eliminated because there are no mechanical components such as ball screws or drive belts.
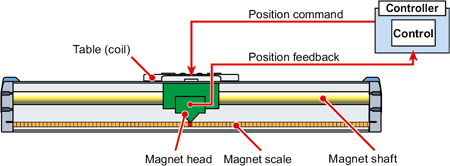
08 Dust preventive structure
All YAMAHA linear motor robots use a stainless steel shutter to prevent dirt and foreign objects from penetrating inside. These shutters are made of tough stainless steel especially designed to withstand an extremely high degree of metal fatigue and made to support long-stroke and highspeed operation.
09 Supports multi-carrier operation
The PHASER series also supports “multi-carrier” operation that allows using 3 or more carriers on one robot. This “multi-carrier” operation is drastically expanding the current range of applications due to its effect in improving tact time and saving space.
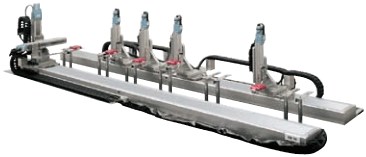
10 Supports dual-drive
Using dual-drive to simultaneously run 2 axes allows highspeed conveyance over a wide area as well as conveying heavy payloads .Yamaha can provide an optimal control system that matches the linkage rigidity of your robot, such as torque support control or bi-axial positioning control.
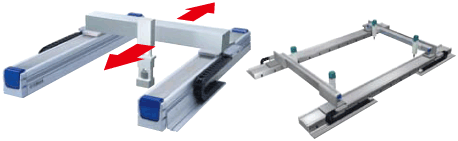
11 Flat type without flying out the cable support is available for the MF7
As the main unit is made compact, a flat type that the cable support is flush with the top surface of the table is available as standard for the MF7.
Select this type according to the tool or workpiece shape or the installation method.
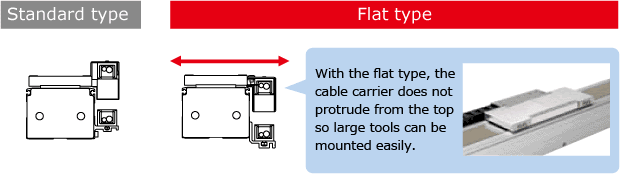
Technical documentation
Funkcje     Specyfikacja
User area